8 Ways to Avoid Costly Crane Repairs
Overhead cranes play a pivotal role in the efficiency of industrial operations, serving as critical equipment in the movement and lifting of heavy materials. However, when these cranes falter, the financial repercussions from repairs, lost productivity, and enhanced safety risks become significant. To effectively manage these expenses and maintain operational continuity, it is imperative to engage in proactive strategies centered around crane repair prevention and preventative crane maintenance. This blog details strategic measures to extend your crane’s lifespan, reduce downtime, and ultimately, avoid costly crane repairs.
The Importance of Safety and Maintenance
Maintaining your crane isn’t just about cost management—it’s fundamentally a safety issue. Crane failures can pose serious safety threats to operators and other workers on site. Regular overhead crane maintenance and adherence to safety protocols minimize the risk of accidents and legal liabilities. Therefore, integrating safety into the maintenance routine is not just good practice—it’s essential for protecting your workforce and your business.
Stick to a Regular Maintenance Schedule
Routine maintenance stands as the cornerstone of effective crane operation and disaster prevention. It is not merely a set of tasks but a systematic, proactive approach aimed at preserving the functionality and safety of your crane equipment. Adhering to the manufacturer’s recommended service intervals is crucial because these guidelines are designed based on thorough testing and knowledge of the equipment’s capabilities and wear characteristics. By following these recommendations, you ensure that every part of the crane is checked and maintained before potential problems arise.
Maintaining organized records of all maintenance activities is equally vital. These records not only provide a clear history of what work has been done but also help in spotting trends or recurring issues that may indicate underlying problems not immediately apparent. Documentation should include details such as the date of maintenance, services performed, parts replaced, and any anomalies noted during checks. This organized approach facilitates traceability and accountability, enabling maintenance teams to act quickly and effectively.
This systematic approach to routine maintenance allows for the early detection of minor issues. For instance, during regular inspections, it may be noticed that a wire rope is beginning to display signs of fraying or that a gear is wearing down unevenly. Identifying these issues early on prevents them from escalating into major faults that can lead to operational failures, costly repairs, or even catastrophic accidents. Thus, routine maintenance is not just a preventive measure against malfunction but also an investment in the crane’s longevity and safety, ensuring that it continues to operate efficiently without unexpected interruptions.
Conduct Daily Operator Checks
A meticulous daily check serves not just to maintain the integrity of the crane but also to reinforce overall workplace safety. By actively searching for and addressing any potential faults, the likelihood of breakdowns occurring mid-operation is dramatically reduced, thereby mitigating the risk of accidents and unplanned downtime which can have serious repercussions for both personnel and productivity. To ensure all bases are covered during the inspection, here’s a detailed list of what to look for.
- Wire Ropes and Chains: Look for fraying, kinks, rust, or any signs of wear that could compromise their strength.
- Hooks: Check for cracks, deformities, or any signs of overloading and make sure the safety latch is functioning correctly.
- Hoist: Examine for smooth operation and listen for any unusual noises that could indicate internal issues.
- Controls: Verify that all buttons, levers, and switches are responsive and correctly labeled, ensuring no sticking or malfunctioning controls.
- Limit Switches and Load Indicators: Test to confirm they are operational and accurate to prevent overloading and overtravel.
- Brakes: Ensure that they are engaging properly and that there is no excessive wear.
- Load Block and End Attachments: Inspect for any signs of damage or twisting that may affect the stability of lifted loads.
- Operator Cab: Check for clear visibility, secure and comfortable seating, and the presence of all necessary operational aids.
- Structural Components: Search for any cracks, bends, or signs of fatigue in the metalwork, including the boom and support structures.
Keep Components Properly Lubricated
Effective lubrication is crucial in reducing friction and preventing wear and overheating of moving parts. Regular application of the correct type of lubricant as per the schedule increases component lifespan and operational efficiency, helping to reduce crane downtime.
Train Operators for Safe Usage
The complexities and risks associated with crane operation demand a robust training program that encompasses various dimensions of safe and proper use. Operator errors, which stand out as a significant cause of crane failures, can be substantially reduced when a workforce is well-versed in the crane’s capacities and the correct operational techniques. Therefore, investing in exhaustive training for crane operators is not only an investment in preventing repairs but also a critical measure for ensuring the safety of everyone on the job site.
A well-rounded crane safety training program should include, but not be limited to, the following types.
- Manufacturer’s Training: Direct instruction on the specific make and model of the crane, covering all operational features and safety recommendations as stated by the manufacturer.
- Load Limits: Education on understanding and adhering to the crane’s load capacity to prevent overloading, which can lead to equipment failure or collapse.
- Proper Lifting Techniques: Training in the principles of hoisting, rigging, and maneuvering loads to minimize stress on the crane structure and mechanisms.
- Emergency Protocols: Instruction on immediate and appropriate responses to potential emergencies, including malfunctions and accidents to minimize harm and damage.
- Hand Signaling and Communication: Learning the standard hand signals and effective communication methods essential for coordinating lifts and ensuring safety when voice communications are not possible.
- Inspection and Maintenance: Teaching operators how to conduct pre- and post-operation inspections and basic maintenance to spot and address any issues before they lead to major problems
Avoid Overloading the Crane
Ensuring that the crane’s weight capacity is always respected is a foundational principle in crane operation safety. Overloading the crane not only jeopardizes the stability and integrity of the crane itself but also poses a significant risk to the safety of the operators and any personnel within the vicinity.
When the specified weight limits are exceeded, the undue strain can compromise the crane’s structural components and mechanical parts, potentially causing catastrophic failures. Such failures not only involve costly repairs and downtime but can also lead to accidents with dire consequences, including injuries or fatalities.
Moreover, the art and science of rigging play a crucial role in the safe and efficient operation of cranes. Correct rigging techniques ensure that loads are securely attached and balanced, thereby preventing slippage, swinging, or accidental release during lifting operations. By applying proper rigging practices, operators can significantly reduce the stress exerted on the crane’s boom, cables, and other critical components.
This not only safeguards the equipment from unnecessary wear and tear but also enhances operational precision and safety. Rigging involves selecting the appropriate slings, chains, ropes, and hooks for the load, considering factors like weight distribution, load materials, and the lifting environment. Rigging also includes the proper calculation of load angles to ensure forces are evenly distributed across the crane structure, minimizing the risk of overloading any single part.
Monitor Electrical Components
Given that electrical failures are a common crane problem, routine inspections of wiring, connections, and control systems are paramount. These checks help spot early signs of issues like overheating, short circuits, or component wear, which could escalate into expensive repairs.
Replace Worn Parts Before They Fail
Ensuring that the crane’s weight capacity is always respected is a foundational principle in crane operation safety. Overloading the crane not only jeopardizes the stability and integrity of the crane itself but also poses a significant risk to the safety of the operators and any personnel within the vicinity. When the specified weight limits are exceeded, the undue strain can compromise the crane’s structural components and mechanical parts, potentially causing catastrophic failures. Such failures not only involve costly repairs and downtime but can also lead to accidents with dire consequences, including injuries or fatalities.
Moreover, certain parts of an overhead crane are more prone to wear and tear and therefore require more frequent inspection and maintenance. These parts include the following.
- Hoist: The hoist is crucial for lifting and lowering loads. Its components, such as the wire rope, drum, and sheaves, endure significant stress during operations, making them susceptible to wear.
- Bearings and gears: These elements facilitate smooth and efficient movement of the crane but can degrade due to continuous friction and load pressure. Regular lubrication and adjustments are necessary to extend their lifespan.
- Wheels and end trucks: Wheels facilitate the movement of the crane along the runway. The wheels and the end trucks they are mounted on can wear down from constant movement, especially if the crane is frequently used or carries heavy loads. Misalignment in the tracking can exacerbate this wear.
- Electrical systems: Overhead cranes rely heavily on their electrical systems to operate. Components like contactors, motors, brakes, and controls can suffer from electrical wear and fatigue. Electrical failures can lead to operational disruptions or pose safety risks.
- Structural components: The crane’s beams, girders, and ties can suffer from stress fatigue and corrosion over time. Structural integrity is vital for safety and must be regularly checked to prevent catastrophic failures.
- Brake system: The brake system is critical for controlling the crane and load during operations. Wear in brakes can lead to uncontrolled movements that are dangerous to both the load and workers.
- Load chain: For cranes that use chains instead of wire ropes, the chain can elongate or wear due to heavy loads and frequent use.
- Control systems: With the increasing adoption of automated and remote control systems in crane operations, these components also require regular updates and maintenance to ensure they function accurately and respond correctly to operator commands.
Understanding the dynamics of the load, including its center of gravity, is imperative in maintaining the crane’s stability throughout the lifting process. Misjudging the center of gravity can lead to the load swinging uncontrollably or tilting, which puts additional stress on the crane and can lead to accidents. Therefore, comprehensive training in load dynamics, alongside adhering to the crane’s weight capacity and employing correct rigging techniques, is indispensable.
Hire Certified Technicians for Inspections
While on-site maintenance is crucial, periodic inspections by certified crane technicians ensure comprehensive evaluations of the crane’s condition. These professionals can identify hidden faults that in-house checks might miss, ensuring compliance with safety standards and extending the crane lifespan.
Implementing these eight steps will significantly contribute to minimizing your crane’s downtime and repair costs. By integrating a culture of preventative crane maintenance and focusing on rigorous training and safety standards, you not only safeguard your investment but also protect your workforce. Taking these proactive measures ensures that your overhead cranes remain reliable, safe, and productive components of your industrial operations.
If you’re ready to enhance your operations with a trusted, precision-engineered crane solution, start your project with us today and experience the Zenar difference. Contact us today to fulfill your custom overhead crane needs.
Read
More
Articles
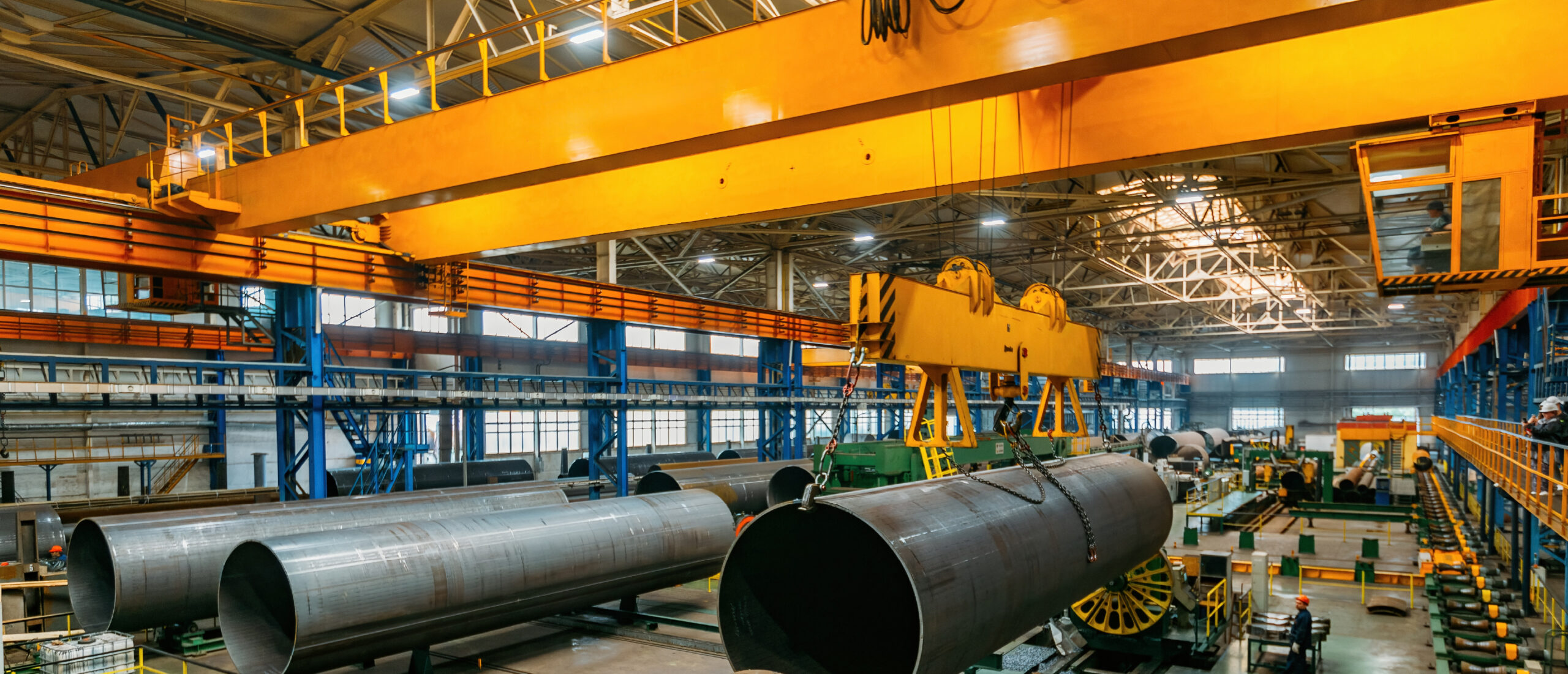
Troubleshooting Techniques for Overhead Crane Electrical Problems
Nestled within the bustling heart of the industrial sphere, overhead cranes stand as monumental testaments to human engineering and ingenuity. These mechanical behemoths are indispensable in a myriad of sectors, from construction to manufacturing, playing a pivotal role in the lifting and transportation of heavy materials. Yet their pivotal role comes with its set of challenges, especially when it comes to maintaining their electrical integrity.
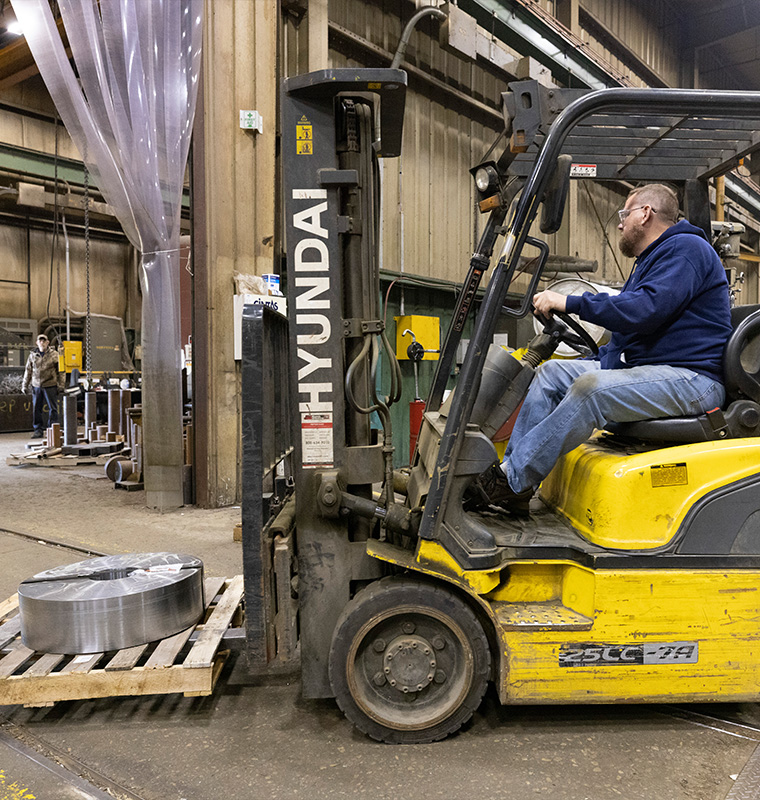
Overhead Cranes vs. Forklifts
When it comes to material handling, efficiency, safety, and cost-effectiveness are always top concerns in any industrial environment. Two of the most common equipment types used in these settings are overhead cranes and forklifts.
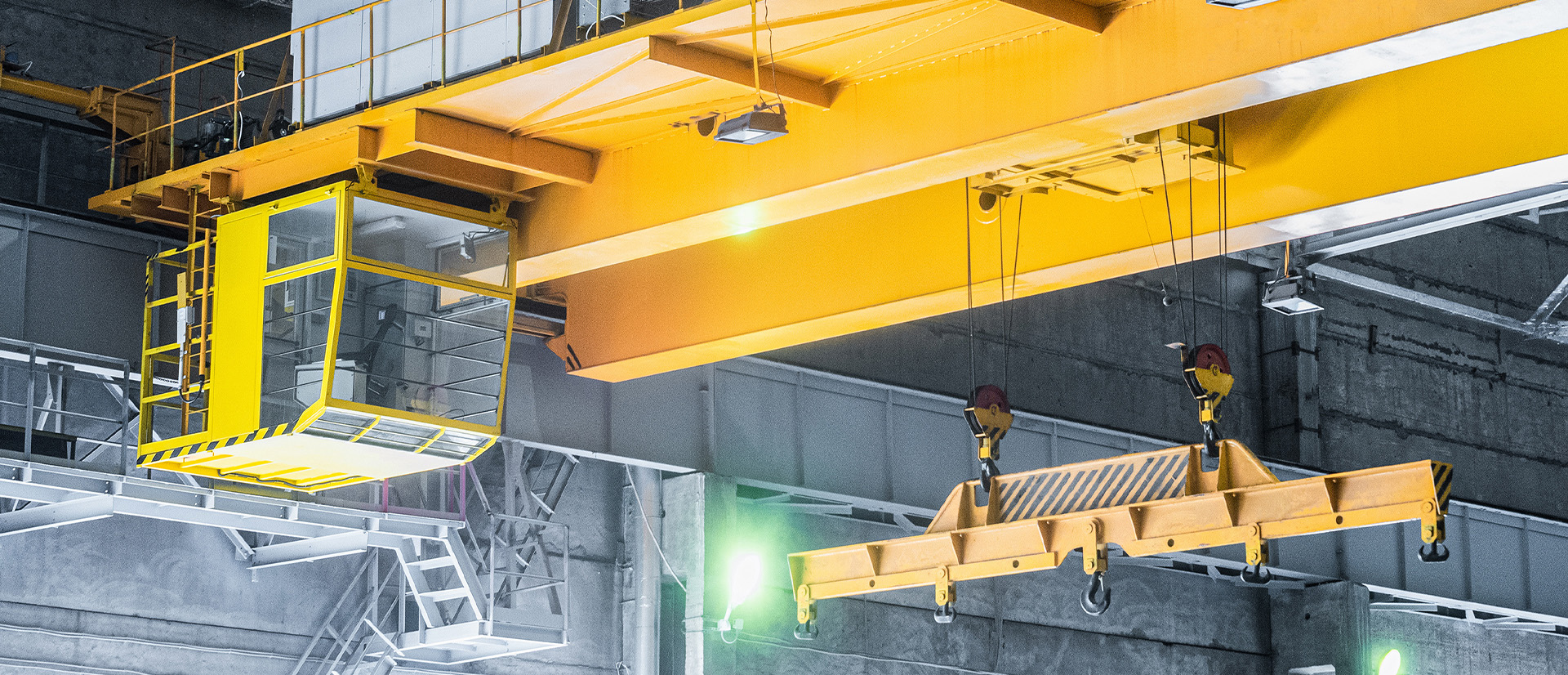
Sustainability in Crane Manufacturing
The construction industry is a cornerstone of global development but is also one of the largest consumers of energy and producers of greenhouse gas emissions.